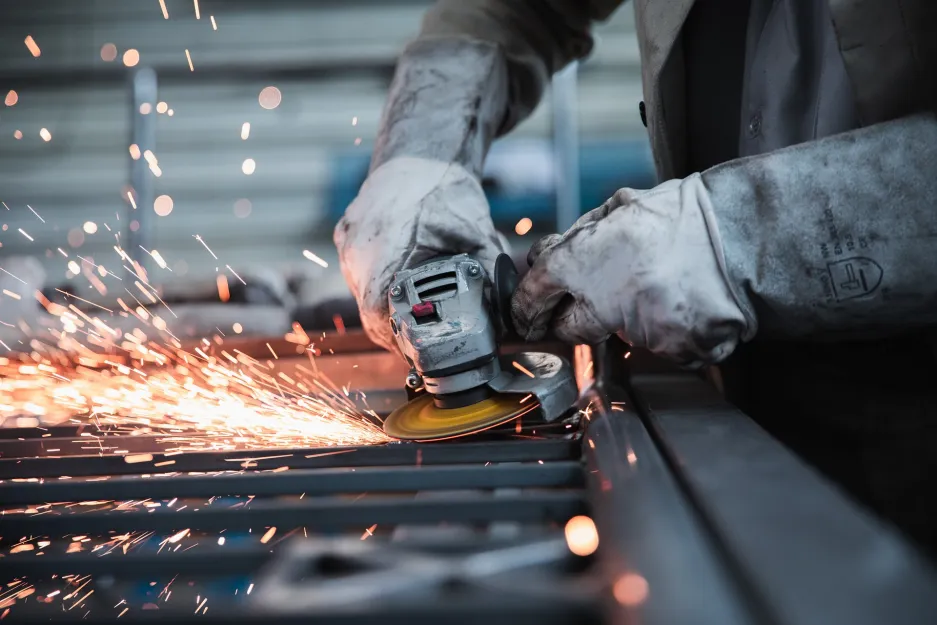
Remanufacturing means making something new again
Published on 19 April 2023
Publication
With the advent of the circular economy, remanufacturing is gaining in popularity. It's not new, but today the planets are aligning: win-win economic models, job creation and resource savings make it a key component of sustainable transition strategies.
First things first: what is remanufacturing? It's literally the "remanufacturing" of a new device from the parts of a used one.
A genuine industrial process
The process comprises five stages, with constant quality assessment as a backdrop - the final tests being crucial for pre-market quality assurance. After an initial assessment of the condition of the device or product, it is disassembled. By the way, the more the design is designed for this from the outset, the easier this stage will be. It is then cleaned and its components sorted. Those that need it are reconditioned or replaced. Finally, the device or product is reassembled and checked.
Sounds simple, but it's actually a complex industrial process! As well as being a technological challenge, it requires high volumes to make the investment in disassembly and assembly lines, test equipment and manpower profitable.
Numerous products and devices
While remanufacturing textile products is hardly conceivable, certain sectors are particularly well-suited to it: products with a high residual value but slow technological evolution.
In the list of sectors concerned, Wallonia certainly has a card to play: aeronautics, automotive, electrical and electronic appliances, office equipment and furniture, heavy equipment excluding road construction, machinery and robots (pumps, machine tools, energy, agri-food, vending machines, etc.), marine industry, medical equipment, rail industry. The list is not exhaustive.
In Mons, for example, the Belgian subsidiary of Japanese equipment manufacturer AISIN remanufactures gearboxes.
Evolving in an ecosystem
"The potential is there, but it's uncharted and difficult territory for many companies," observes Patrick Van den Bossche, Lead Sustainability at the Belgian federation of technology companies (Agoria). "You don't have to do everything yourself, but look for partners. You have to work in an ecosystem and take a multidisciplinary approach," he advises.
Logistics is a real challenge, because to be able to remanufacture them, you have to get the products back at the end of their life. In conventional sales, they disappear. So we need to rethink the value chain and maintain or establish a link with the end customer. The functionality economy, where the manufacturer retains ownership of the product and merely sells a service, offers possible synergies.
Saving materials makes sense
Remanufacturing is a "green giant" that is all too often overlooked. It saves an average of 85% of the energy used in a product, which would be lost if it were recycled as raw material. It doesn't prolong its life cycle, but starts a new one.
It creates jobs: even if certain processes can be robotized, as in the case of cell phones, it takes three to five times as many people as to manufacture new products.
And it's still profitable! "We spend most of our attention on manpower, but if we do the same on materials, the gain is incredible, and we become truly competitive on the export market", enthuses P. Van den Bossche. The same product, "as new" (or even improved), will ultimately be remanufactured at a reduced cost of materials. This is because the added value already present in the product is retained, potentially offsetting the additional cost of labor. "And don't worry: quite often there's an entirely different market for remanufactured products, which doesn't cannibalize the market for new products", he reassures us.